Discover everything about AL6061 aluminum CNC machining—its properties, advantages, applications, and best machining practices to achieve high-quality results.
Aluminum is one of the most widely used materials in CNC machining, and AL6061 aluminum stands out as a top choice. Its versatility, strength, and ease of machining make it ideal for various industries. But what makes AL6061 so special? In this guide, we’ll explore its properties, applications, advantages, and machining best practices.
AL6061 Aluminum CNC Machining
CNC machining is a precise and efficient method for producing custom aluminum parts. AL6061 aluminum CNC machining is favored due to its excellent machinability and balance of mechanical properties. Whether for prototyping or mass production, this alloy ensures high performance and durability.
Benefits of Using AL6061 in CNC Machining
Excellent Strength-to-Weight Ratio – Provides durability without excess weight.
Corrosion Resistance – Performs well in harsh environments.
Good Thermal Conductivity – Ideal for heat-sensitive applications.
Ease of Machining – Reduces tool wear and increases efficiency.
Key Properties of AL6061 Aluminum
Mechanical Properties
Tensile Strength: 310 MPa
Yield Strength: 276 MPa
Hardness: 95 Brinell
Density: 2.7 g/cm³
Corrosion Resistance
AL6061 has excellent resistance to oxidation and corrosion, making it perfect for outdoor and marine applications.
Heat Treatability and Machinability
Easily heat-treated to enhance strength.
Great machinability
Allowing for tight tolerances in CNC machining.
Comparison: AL6061 vs. Other Aluminum Alloys
Property | AL6061 | AL7075 | AL5052 | AL2024 |
Strength | Medium | High | Low | Very High |
Corrosion Resistance | High | Moderate | Very High | Low |
Machinability | Excellent | Moderate | Good | Difficult |
Cost | Moderate | High | Low | High |
Advantages of Using AL6061 for CNC Machining
1. Strength-to-Weight Ratio
2. Lightweight yet strong, making it ideal for aerospace and automotive applications.
3. Ease of Machining
4. Can be cut, drilled, and shaped efficiently with minimal tool wear.
5. Cost-Effectiveness and Availability,widely available and competitively priced compared to other aluminum alloys.
Challenges in CNC Machining AL6061 Aluminum
Common Machining Difficulties
— Tool wear due to aluminum’s abrasiveness.
— Chatter and vibration affecting surface finish.
Overcoming Tool Wear and Chatter
— Use carbide tools for better longevity.
— Optimize feed rates and cutting speeds.
Best Practices for Precision Machining
— Apply coolant to reduce heat buildup.
— Use sharp tools for clean cuts.
Best Applications of AL6061 in CNC Machining
— Aerospace and Automotive Components
— Aircraft structural parts
— Car chassis and engine components
— Electronics and Consumer Goods
— Laptop casings
— Camera parts
— Industrial Machinery and Structural Applications
— Hydraulic systems
— Machine frames
Surface Finishing Options for AL6061 Machined Parts
Anodizing for Durability
Anodizing is a popular surface treatment for AL6061 machined parts, improving corrosion resistance, wear resistance, and aesthetics. It involves creating an oxide layer on the aluminum surface through an electrochemical process. There are different types of anodizing:
Type I (Chromic Acid Anodizing): Thin coating, excellent for corrosion resistance.
Type II (Sulfuric Acid Anodizing): Medium thickness, available in various colors.
Type III (Hard Anodizing): Thickest coating, superior hardness and durability.
Common Anodizing Colors for AL6061
Natural (Clear), Black, Red, Blue, Gold,Green.
Anodizing not only enhances durability but also improves the aesthetic appeal of AL6061 components.
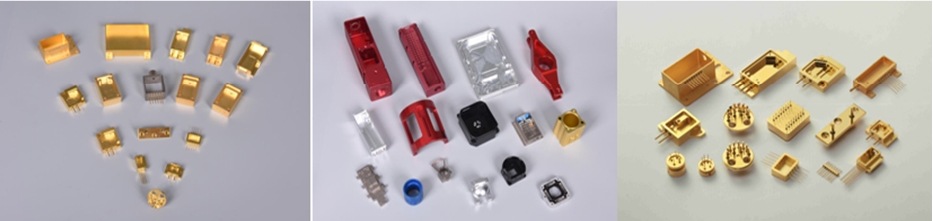
Chemfilm (Chromate Conversion Coating)
Chemfilm, also known as chromate conversion coating, is another surface treatment used for AL6061 aluminum. Unlike anodizing, which builds up an oxide layer, Chemfilm creates a thin, corrosion-resistant coating without significantly affecting electrical conductivity.
Difference Between Chemfilm and Anodizing
Feature | Anodizing | Chemfilm (Chromate Conversion) |
Coating Thickness | 2-50 microns | 0.5-4 microns |
Corrosion Resistance | High | Moderate |
Color Options | Multiple (Black, Blue, Red, etc.) | Yellow, Clear |
Electrical Conductivity | Non-conductive | Conductive |
Durability | High | Moderate |
Chemfilm is preferred when electrical conductivity must be preserved, while anodizing is ideal for high wear resistance and aesthetics.
Powder Coating and Painting
— Enhances aesthetic appeal and adds extra protection.
— Polishing and Bead Blasting
— Creates a smooth, reflective surface ideal for consumer products.
Cost Factors in AL6061 Aluminum CNC Machining
Raw Material Costs
AL6061 is affordable but varies based on supply chain fluctuations.
Machining Time and Complexity
Longer machining times increase costs, so optimizing parameters is crucial.
Post-Processing Expenses
Additional finishes like anodizing or coating add to the final cost.
Types of AL6061 Material and Common Sizes in the Chinese Market
AL6061 aluminum is available in various forms to suit different machining needs. Get to know the most common types and their standard sizes in the Chinese market.
The availability of these sizes makes it easy for manufacturers to choose the right material for their CNC machining projects.
FAQs
Is AL6061 the best aluminum for CNC machining?
— AL6061 is one of the best due to its machinability, strength, and affordability, but the choice depends on the application.
How does AL6061 compare to AL7075 in strength?
— AL7075 is stronger but less corrosion-resistant and harder to machine.
What is the best way to finish AL6061 parts?
— Anodizing is recommended for durability, while polishing is ideal for aesthetics.
Can AL6061 be welded easily?
— Yes, it can be welded, but proper post-weld heat treatment is needed for optimal strength.
What industries use AL6061 aluminum the most?
— Aerospace, automotive, electronics, and industrial sectors.
How to reduce machining costs for AL6061 aluminum?
— Optimize cutting speeds, use carbide tools, and minimize post-processing.
Conclusion
AL6061 aluminum is a top-tier material for CNC machining, offering an exceptional balance of strength, corrosion resistance, and affordability. Whether for aerospace, automotive, or consumer electronics, its versatility makes it a go-to choice. By following the best machining practices and selecting the right finishing methods, manufacturers can ensure high-quality, cost-effective parts.
Unlock the potential of AL6061 aluminum CNC machining today!