Paint and Powder Coating Services
Home » Surface Finishing Services » Paint and Powder Coating Services
High quality paint and powder coating service in China.
SYM offers paint and powder coating as a value-added service to cnc machining parts, welding parts and sheet metal fabrication. SYM provides powder coating services in a variety of colors, such as red, orange, blue, black, and several other colors.
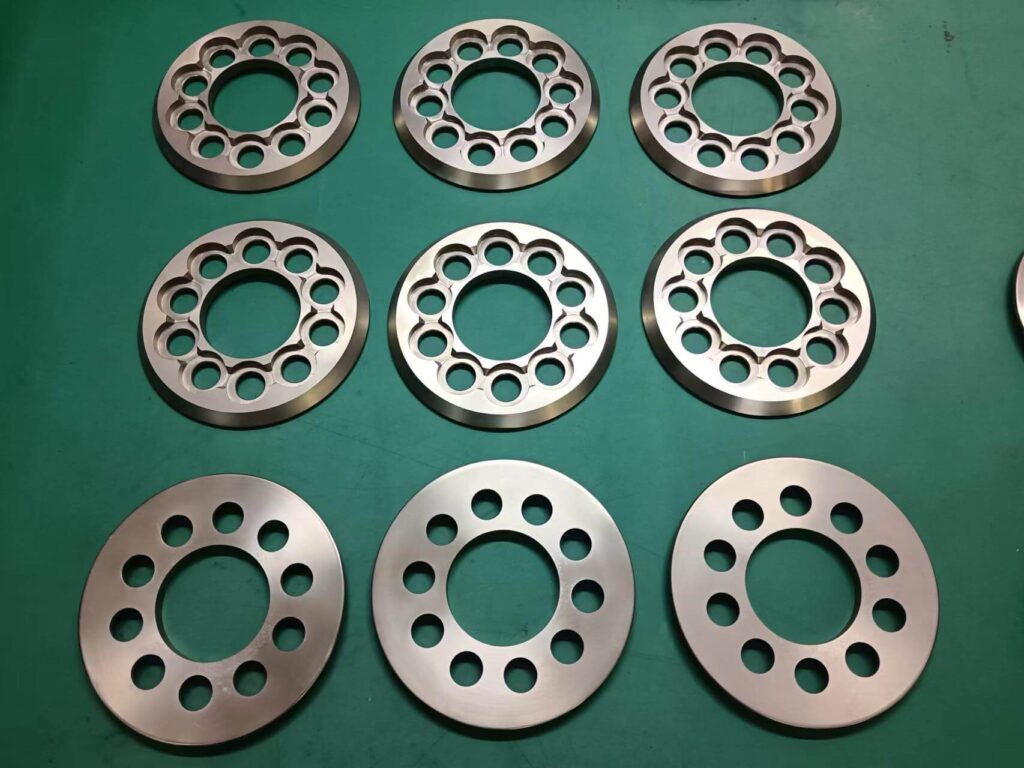
The normal material we used for optical mounts and housings
Aluminum alloy
Lightweight and easily machinable, aluminum is often used for optical mounts, housings, and frames. It can also be anodized for better corrosion resistance.
Stainless Steel
Provides strength and corrosion resistance for optical mounts in harsh environments.
Titanium
Used in applications requiring high strength-to-weight ratios and thermal stability, such as space optics.
How Powder Coating Works?
Surface Preparation
The part is thoroughly cleaned to remove any dirt, oil, or oxidation. This is essential for proper adhesion of the powder.
Application
An electrostatic gun sprays the powder onto the part. The powder particles are charged, helping them stick to the grounded surface.
Curing
The part is heated in an oven where the powder melts, flows, and forms a uniform, solid layer that bonds to the surface.
Advantages of Powder Coating
Electroplating services can be applied to a range of materials, but certain metals and conductive materials are particularly well-suited for achieving quality, durable finishes. Metals Commonly Used for Electroplating.
Durability
Powder coating creates a tough, scratch-resistant surface that’s ideal for high-wear applications.
Corrosion Resistance
It offers excellent resistance to rust, moisture, and chemicals, making it suitable for outdoor use.
Wide Color and Texture Options
Powder coating is available in numerous colors and finishes, from high gloss to matte, and even textured effects.
Environmentally Friendly
Powder coating produces less waste and has fewer harmful emissions than traditional liquid paint.
Applications of Powder Coating
Powder coating provides a durable, attractive, and environmentally friendly finish ideal for a wide range of applications across industries.
Automotive and Motorcycle Parts
Rims, frames, and other parts are powder-coated for durability and style.
Appliances
Refrigerators, washers, and dryers use powder coating for a sleek, long-lasting finish.
Furniture
Metal furniture, both indoor and outdoor, is powder-coated for added weather resistance and a polished look.
Industrial Equipment
Machinery parts and tools are powder-coated to protect them from harsh working conditions.
What is paint service?
Paint services refer to applying a liquid coating to a surface for protection, aesthetics, or both. The paint, which typically consists of pigments, binders, and solvents, is sprayed, brushed, or dipped onto a material, creating a smooth or textured finish after it dries or cures. Painted surfaces can be found everywhere, from vehicles and buildings to appliances and furniture.
Differences between Paint and Powder Coating service:
Feature | Paint Service | Powder Coating Service |
Application | Liquid paint is applied with a spray, brush, or roller. | Powder is applied using an electrostatic spray gun. |
Drying/Curing Process | Air-dried or low-temperature baked. | Cured in an oven at higher temperatures. |
Thickness of | Generally thinner; multiple coats may be needed. | Forms a thicker, single coat. |
Durability | More prone to chipping, scratching, and fading. | Highly durable, scratch-resistant, and weatherproof. |
Finish Options | Wide range of colors, gloss levels, and textures. | Also has many color and texture options, often with higher gloss and consistency. |
Environmental Impact | Typically contains VOCs (volatile organic compounds). | Lower emissions and waste, with no VOCs. |
Cost | Usually more affordable, especially for small jobs. | Often higher initial cost but may be cost-effective in the long run due to durability. |
Which to Choose?
Use Paint When
You need more flexibility in color or finish choices, lower cost for smaller jobs, or a thinner coating. It’s also ideal for materials that can’t tolerate high curing temperatures.
Use Powder Coating When
Durability and weather resistance are crucial, as in outdoor and high-wear applications. Powder coating is also preferred when an eco-friendly process with fewer emissions is required.
How Powder Coating Affects Tolerance?
Powder coating adds a layer of material to the surface of a part, which affects the dimensions and tolerance of machined parts. The thickness of the powder coating varies based on the application and type of powder used, but it typically ranges from 0.001 to 0.004 inches (25 to 100 microns) per layer. This thickness needs to be considered when designing or machining parts, especially for parts with tight tolerances or precise fits.
Coating Thickness Adds to Dimensions
Powder coating builds up on all coated surfaces, meaning that the final dimensions of a part will be larger than the original machined dimensions. For parts with critical tolerances, this added thickness must be taken into account to avoid interference or misalignment.
Post-Machining May Be Required
For certain applications, critical surfaces or holes may require post-machining after powder coating to ensure that tight tolerances are met. This is often necessary for mating parts, threaded holes, or areas where precise fits are essential.
Masking Options for Critical Surfaces
Masking can be used on areas that need to remain coating-free. By masking threaded holes, bearing surfaces, or other critical features, you can maintain the original machined tolerances without needing further modification after coating
General Guidelines for Machined Part Tolerances with Powder Coating
By accounting for the added thickness of powder coating in the design and manufacturing stages, you can ensure that your parts meet final tolerance requirements without compromising functionality or fit.
Standard Thickness Allowance
For general applications, allow for an increase in thickness of 0.002 to 0.008 inches (50 to 200 microns) in your tolerance calculations.
Tight Tolerance Parts
For parts with tolerances tighter than ±0.001 inches (±25 microns), consider masking critical areas or performing additional machining after coating..
Design Adjustments
Get Your Parts Into Production Today!
Want to learn more about SYM precision machining services, please contact us now.