Wire EDM Machining Services
Home » Wire EDM Machining Services
One stop Wire EDM Machining Services from china factory
World leader in wire EDM machining, supplying high-precision prototypes for your machining needs.
We offer wire EDM and sinker EDM, precision EDM machining at the highest level.
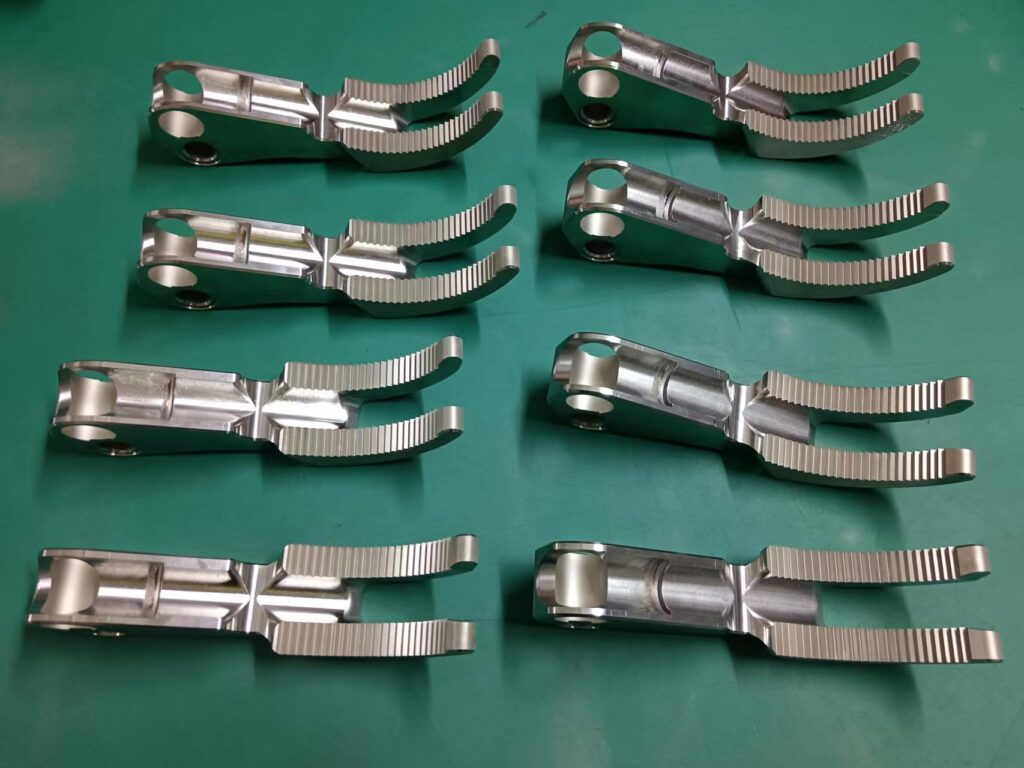
What is Wire EDM Machining Services?
Wire Electrical Discharge Machining (EDM) is a precision manufacturing process that uses electrical discharges to remove material from a workpiece. Here are key aspects of Wire EDM machining services
High precision
Wire EDM can achieve extremely tight tolerances, often within ±0.0001 inches (±2.54 microns).
Complex geometries
Capable of cutting intricate shapes and internal features that would be difficult or impossible with traditional machining methods.
Suitable for hard materials
Effective for cutting hardened steels, titanium, and other tough alloys.
Smooth surface finish
Produces excellent surface finishes, often requiring minimal post-processing.
Applications of Wire EDM Machining
Wire EDM is particularly valuable in industries such as aerospace, medical device manufacturing, and tool making, where precision and complex geometries are crucial.
Cutting precise slots and openings in metal parts
Manufacturing intricate stamping dies and molds
Producing small, delicate parts for medical devices
Creating custom gears and sprockets
Fabricating aerospace components with complex geometries
EDM Surface Characteristics
The surface finish produced by EDM (Electrical Discharge Machining) can vary depending on the specific type of EDM process used
Wire EDM
Generally produces a smooth surface finish. The surface roughness can typically range from 0.8 to 1.6 μm Ra, but can be as low as 0.1 μm Ra with multiple skim cuts.
Sinker EDM
Can produce surfaces ranging from very smooth to intentionally textured, depending on the parameters used. Roughness can vary from about 0.4 to 50 μm Ra.
The presence of tool marks in EDM depends on several factors
- For Wire EDM, visible lines may appear on the cut surface, representing the path of the wire. These are typically very fine and can often be minimized with proper machine settings.
- In Sinker EDM, the surface may show a slight "orange peel" texture or small craters, which are characteristic of the spark erosion process.
The final surface finish in EDM is influenced by factors such as the machine parameters, electrode material, dielectric fluid, and the number of finishing passes. By adjusting these factors, manufacturers can achieve the desired balance between surface smoothness and production efficiency.

Types of Wire EDM Cutting
Wire EDM cutting can be categorized into three main types based on the cutting speed.
Fast Wire Cutting
Fast wire cutting is used for rough cuts and initial shaping of parts. It offers:
- Higher cutting speeds
- Reduced precision compared to slower cuts
- Suitable for larger parts or when time is a critical factor
- Surface Roughness: Typically 3.2 to 6.3 μm Ra
- Accuracy: ±0.025 to ±0.05 mm (0.001" to 0.002")
Medium Speed Cutting
Medium speed cutting provides a balance between speed and precision. It is characterized by:
- Medium speed cutting provides a balance between speed and precision. It is characterized by:
- Better surface finish than fast cutting
- Suitable for general purpose EDM work
- Surface Roughness: Usually 1.6 to 3.2 μm Ra
- Accuracy: ±0.010 to ±0.025 mm (0.0004" to 0.001")
Slow Wire Cutting
Slow wire cutting is used for high-precision work and finishing cuts. It offers:
- Slower cutting speeds
- Highest level of precision and surface finish
- Ideal for parts requiring tight tolerances or superior surface quality
- Surface Roughness: Can achieve 0.4 to 1.6 μm Ra or better
- Accuracy: ±0.002 to ±0.010 mm (0.0001" to 0.0004")
The choice between these cutting types depends on the specific requirements of the part, including tolerance levels, surface finish needs, and production time constraints. Often, a combination of these cutting types is used in a single part, starting with fast cutting for rough shaping and progressing to slow cutting for final precision work.
It’s important to note that these values can vary depending on the specific machine, wire type, workpiece material, and other process parameters. The trade-off between cutting speed, surface finish, and accuracy allows manufacturers to choose the most suitable approach for each application.
SYM Wire EDM Machining services capacity.
There are 10 set of Wire EDM machine and 4 set of Sinker EDM machine at SYM machining factory
At SYM precision machining factory, we have 10 set of Wire EDM machine and 4 set of Sinker EDM machine in house, with 25 years experiences in precision machining industry, combine cnc machining process, and precision grinding process, we can provide you one-stop machining solution for your precision engineering requirements. Order quantity from 1 unit to over 500 units, customized precision components meet to your drawing specifications on time, every time.
M/C Type | Qty’ | Brand | Made in | Model | X/Y/Z Travel | Accuracy |
Wire EDM | 1 | SODICK | JAPAN | AQ560L | 560 X 350 X 300 | 0.002 |
| 1 | SODICK | JAPAN | ALN400QS | 400 X 300 X 250 | 0.002 |
| 2 | SODICK | JAPAN | ALN400Q | 400 X 300 X 250 | 0.002 |
| 2 | SODICK | JAPAN | AQ400LS | 400 X 300 X 250 | 0.002 |
| 1 | SODICK | JAPAN | AQ360LS | 360 X 250 X 250 | 0.002 |
| 1 | SEIBU | JAPAN | M50B | 500 X 350 X 310 | 0.002 |
| 2 | SSG | TAIWAN | LA500A | 500 X 350 X 270 | 0.005 |
Sinker EDM | 4 | TAISHU | TAIWAN | XH-450 | 450 X 300 X 300 | 0.01 |