Quality Control
Home » Quality Policy
Quality control for high precision machining services, excellence in every step
For nearly 25 years, SYM Precision Machining has been at the forefront of high-precision machining services. Over the years, we have continuously improved and refined our processes to meet the ever-evolving needs of our customers. By establishing a comprehensive in-house quality management system, we ensure that every part we deliver meets the highest standards of precision and reliability.
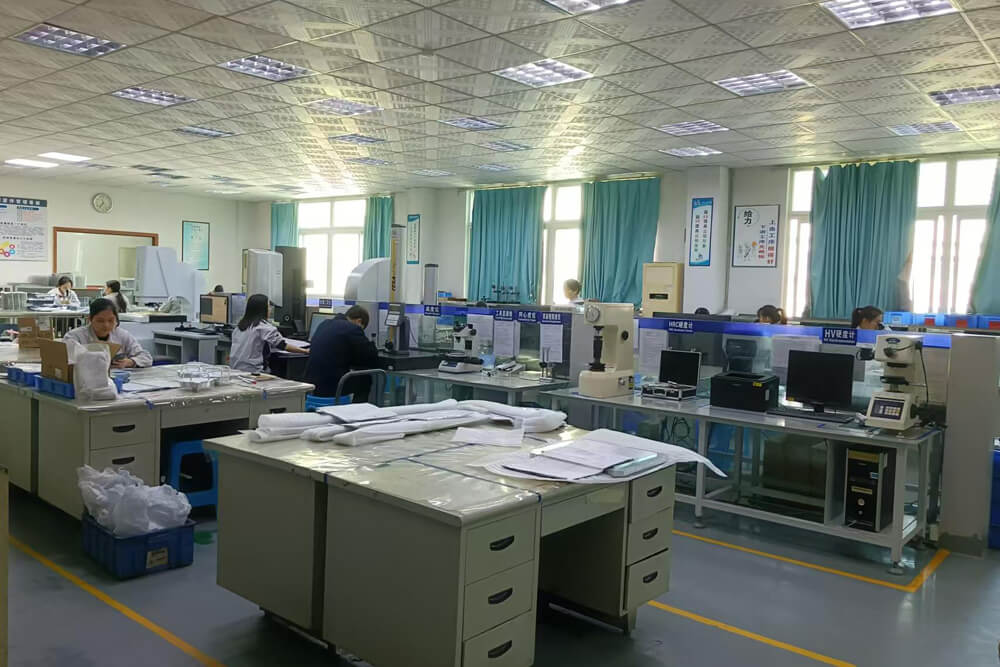
Quality Certifications
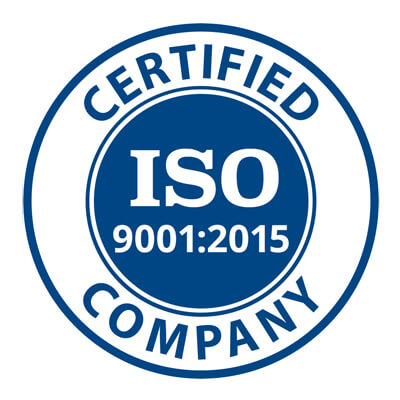
ISO 9001
General quality management standards.
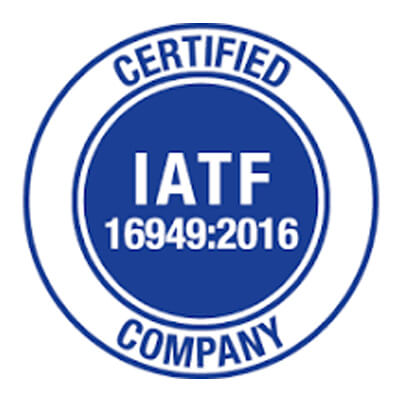
IATF 16949
Automotive industry-specific requirements.
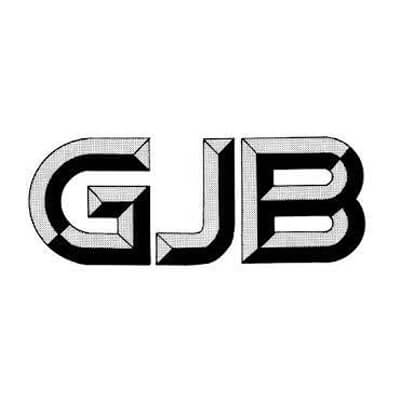
GJB91001C-2017
Military quality management standards.
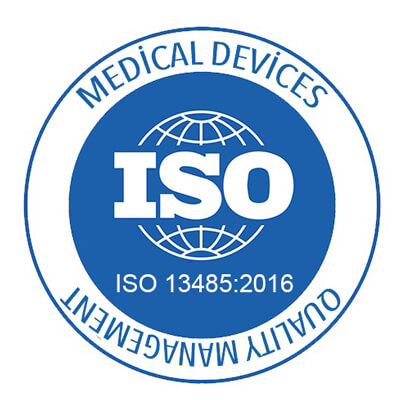
ISO 13485:2016
Medical device quality management systems.
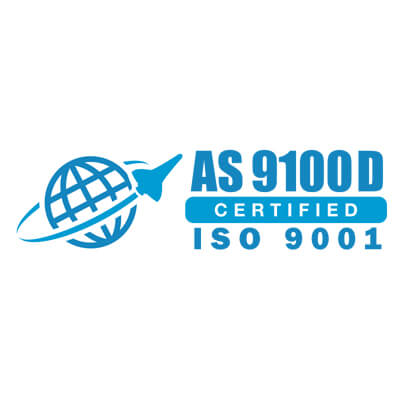
AS9100D EN9001:2018
Aerospace industry quality standards.
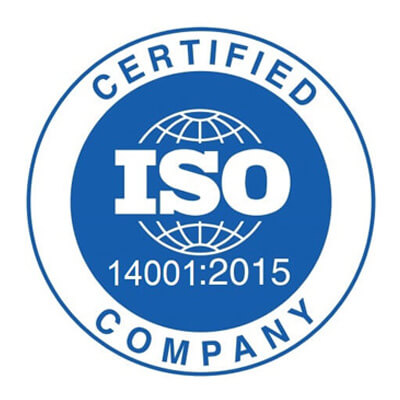
ISO 14001:2015
Environmental management systems.
Quality Control Process
Our quality assurance system is implemented at every stage of production
Incoming Quality Control (IQC)
Inspect all raw materials to ensure they meet required specifications.
In-Process Quality Control (IPQC)
Monitor production processes to identify and resolve issues in real time.
First Article Inspection (FAI)
Verify the accuracy and quality of the first production part to set the standard for the batch.
Quality Assurance (QA)
4.Conduct final inspections before shipment to ensure all products meet customer requirements.
Experienced Quality Team
Our quality assurance system is implemented at every stage of production
- Incoming Material Inspection: Verifies raw materials comply with specifications.
- Process Inspection: Monitors production quality at every step
- Final Delivery Inspection: Ensures all finished products meet standards before shipping
- Quality Engineers: Develop and maintain quality systems, analyze data, and implement improvements
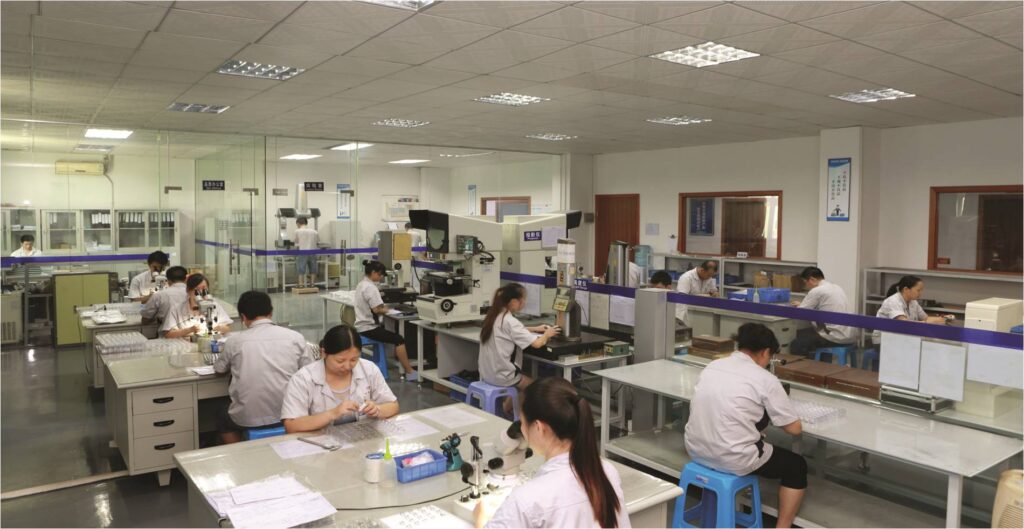
Advanced Measuring Equipment
To guarantee precise and accurate results, SYM utilizes cutting-edge measuring tools, including
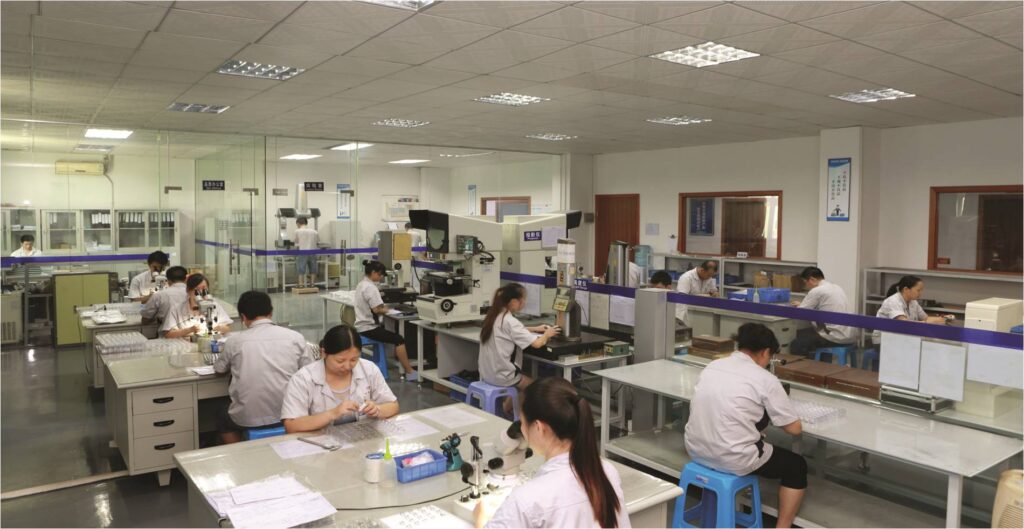
- Coordinate Measuring Machine (CMM): For detailed 3D measurements.
- Height Gage: Accurate vertical measurements
- 2D Vision Measuring Machine: Non-contact measurements for complex geometries
- Profile Projector: Visual inspection of intricate profiles
- Stationary Metal Analyzer: Ensures material composition accuracy
- Hardness Tester: Measures material hardness for durability verification
- Coating Thickness Gauge: Ensures even plating or coating thickness
- Surface Roughness Gauge: Verifies surface finishes
- Concentricity Gauge: Measures alignment precision of circular features
- Pin Gauge and Steel Gauge Blocks: For holes diameter and precise slot dimensional checks
- Calipers and Digital Micrometers: General-purpose precision measurements
M/C Type | Qty’ | Brand | Made in | Model | Measuring Range (mm) | Accuracy (mm) |
CMM | 1 | ZEISS | GERMANY | SPECTRUM 10/12/6 | 800 X 1200 X 900 | 1.7+L/350um |
1 | TESA | SWITZERLAND | Micro-Hite 3D | 460 X 510 X 420 | 0.003 | |
Height Gage | 6 | TESA | SWITZERLAND | Hite 700/400/350 | 0-700 | 0.002 |
2.5D Auto Vision Measuring Machine | 1 | GDH | CHINA | 3020CNC | 300 X 200 X 200 | 0.003 |
2D Vision Measuring Machine | 8 | EASSON | CHINA | VMS-1510G | 150X 110 X 100 | 0.01 |
Profile Projector | 2 | RATIONAL | CHINA | CPJ-3050 | 150 X 50 X 100 | 0.005 |
Digital Micrometer | 24 | QLR | CHINA | 0-75 | 0.004 | |
Digital Three Point Internal Micrometer | 2 | MITUTOYO | JAPAN | SBM-63CX/88CX | 55~63/75~88 | ±0.006 |
Three Point Internal Micrometer | 24 | QLR | CHINA | 6-100mm | 6-100 | ±0.005 |
Tungesten Steel Gauge Block | 1 | AVIC | CHINA | 0.5-100mm | 0.50-100 | 0.002 |
Concentricity Gauge | 1 | UNIVERSAL | AMERICA | 23211-B-10P | Φ3~ Φ25 X 102 mm | 0.002 |
Measuring Microscope | 3 | MITUTOYO | JAPAN | TM505 | 50 X 50 X 115 | 30X |
Surface Roughness Gauge | 2 | MITUTOYO | JAPAN | SJ-201 | -200~+150 mm | – |
Stationary Metal Analyzer | 1 | AMETEK | GERMANY | SPECTROMAXx | – | – |
X-ray Coating Thickness Gauge | 1 | MicroPioneer | KOREA | XRF-2000 | 0-30 (H) | 0.01 um |
Vickers Hardness Tester | 1 | SCTMC | CHINA | HV-1000 | 1-2967 HV | 0.01 |
Rockwell Hardness Tester | 2 | ROCKIE | CHINA | HR-150A | 20-88HRA | 20-100HRB 20-70 HRC | 0.5HR |
SYM Precision Machining Inspection Guide
1. 100% Appearance Inspection
- All parts undergo 100% visual inspectionto detect surface defects such as: scratches, burrs, dents, finish imperfections.
- Ensures the aesthetic quality of every part meets customer expectations.
2. Dimensional Inspection
- For Sample Size Production: Full Inspection, all dimensions of each part are inspected to verify compliance with design specifications.
- For Mass Production: Sampling Inspection, Conducted based on the AQL MIL-STD-105E sampling standard. Except for the special requirements of customers, we inspect the machined parts according to typically 0.25 to 0.4 for critical dimensions. Sampling size and criteria determined according to lot size and inspection level.
3. Key Characters Inspection
- Threads: Inspection for pitch, angle, and fit using thread gauges.
- Precision Shaft and Hole Sizes: Checked using micrometers, PINgauges, and CMMs for tight tolerances.
- Shape and Position Tolerance:Flatness, perpendicularity, concentricity, and other geometric tolerances measured using profile projectors, CMMs, or special gauges.
Documentation and Compliance
Raw Material Certifications
Proof of material composition and quality.
Certificate of Conformance (COC)
Confirms compliance with customer specifications.
Plating and Finish Documents
Details about surface treatments.
Dimensional Inspection Documents (QA Reports)
Records of inspected dimensions.
RoHS & REACH Compliance
Environmental and safety certifications
Key Highlights of SYM's Quality Management System
Continuous Improvement
We regularly review and enhance our processes to ensure we stay ahead in precision machining technology.
Certified Quality Standards
Our quality management system is certified to ISO 9001, IATF 16949, ISO 13485, AS9100D, and other international standards, demonstrating our commitment to excellence across industries.
Comprehensive Inspections
From raw materials to final product delivery, every step undergoes rigorous inspection to guarantee flawless results.
State-of-the-Art Equipment
We use advanced CNC machines and precision measuring tools to achieve unparalleled accuracy and consistency.